Professional Suggestions on What is Porosity in Welding and How to Resolve It
Comprehending Porosity in Welding: Exploring Causes, Effects, and Prevention Strategies
As specialists in the welding sector are well conscious, understanding the reasons, impacts, and avoidance methods related to porosity is essential for attaining durable and dependable welds. By delving into the root causes of porosity, analyzing its detrimental effects on weld quality, and discovering effective prevention approaches, welders can boost their knowledge and abilities to create high-grade welds constantly.
Usual Reasons For Porosity
Contamination, in the type of dust, oil, or corrosion on the welding surface area, creates gas pockets when heated, leading to porosity in the weld. Improper shielding takes place when the shielding gas, typically made use of in procedures like MIG and TIG welding, is incapable to completely safeguard the liquified weld pool from responding with the bordering air, resulting in gas entrapment and subsequent porosity. In addition, inadequate gas coverage, typically due to incorrect flow prices or nozzle positioning, can leave parts of the weld vulnerable, allowing porosity to create.
Impacts on Weld High Quality
The presence of porosity in a weld can substantially compromise the general top quality and stability of the welded joint. Porosity within a weld creates spaces or dental caries that damage the structure, making it more prone to fracturing, deterioration, and mechanical failing.
Furthermore, porosity can impede the performance of non-destructive screening (NDT) strategies, making it testing to detect other problems or suspensions within the weld. This can cause considerable safety and security issues, specifically in important applications where the architectural integrity of the welded parts is paramount.
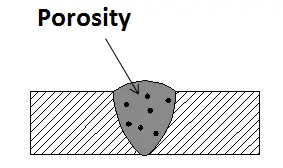
Avoidance Techniques Review
Offered the destructive effect of porosity on weld quality, efficient prevention strategies are vital to preserving the structural stability of bonded joints. Furthermore, picking the appropriate welding specifications, such as voltage, current, and take a trip rate, can help decrease the threat of porosity development. By incorporating these prevention techniques into welding methods, the incident of porosity can be dramatically reduced, leading to more powerful and extra trusted bonded joints.
Importance of Proper Shielding
Correct securing in welding plays an essential role in stopping atmospheric contamination and making sure the honesty of bonded more helpful hints joints. Securing gases, such as argon, helium, or a mixture of both, are typically used to secure the weld swimming pool from reacting with components in the air like oxygen and nitrogen. When these reactive elements enter contact with the hot weld pool, they can cause porosity, resulting in weak welds with minimized mechanical buildings.

Insufficient shielding can cause numerous problems like porosity, spatter, and oxidation, jeopardizing the structural integrity of the bonded joint. Therefore, adhering to proper securing practices is vital to produce top notch welds with this page very little problems and make certain the durability and reliability of the welded elements (What is Porosity).
Tracking and Control Approaches
Exactly how can welders effectively keep track of and manage the welding process to guarantee optimal results and stop issues like porosity? By continuously checking these variables, welders can determine deviations from the ideal conditions and make instant adjustments to stop porosity formation.

In addition, carrying out correct training programs for welders is crucial for keeping an eye on and controlling the welding process effectively. What is Porosity. Informing welders on the value of maintaining constant parameters, such as correct gas protecting and travel speed, can assist avoid porosity problems. Regular evaluations and qualifications can likewise ensure that welders excel in surveillance and regulating welding procedures
In addition, making use of automated welding systems can boost monitoring and control capabilities. These systems can precisely control welding parameters, reducing the possibility of human mistake and making certain consistent weld high quality. By combining innovative monitoring technologies, training programs, and automated systems, welders can effectively check and regulate the welding process to lessen porosity problems and accomplish premium welds.
Conclusion
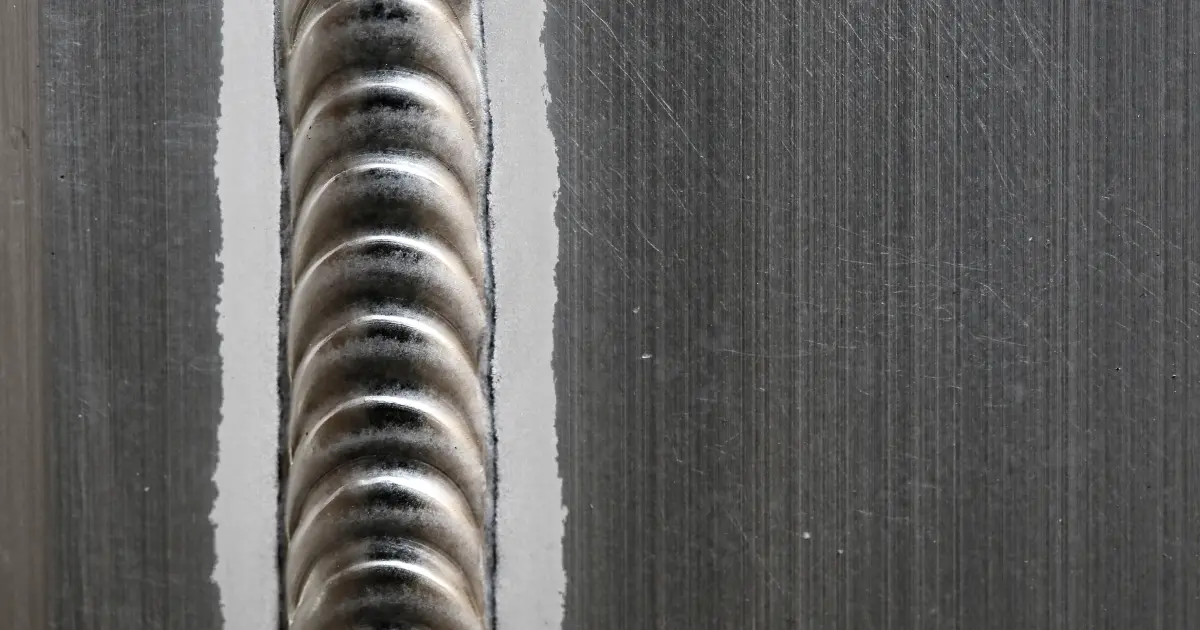